ディップコーティングの考え方
ディップコーティングによるワークへの膜厚は、引き上げ速度とコート液の粘度によって決まってきます。
以下の関係式を用いることでウェット状態ににはなりますが、ディップコーティングを行う前の凡その目安となります。
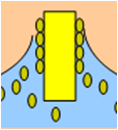
引き上げ速度と膜厚の関係式
ディップコーティングにおける引き上げ速度と膜厚には以下の関係式が成り立ちます。
引き上げ速度が速く粘度が高い場合は、

引き上げ速度が非常に遅く、粘度が低い場合は、

ここでは、Cは係数(ニュートン流体では0.8)、Vは引き上げ速度、ηは動粘度、ρは液粘度、γは液の表面張力とする。
※ウェット時の膜厚理論値となります。
乾燥や周囲環境の影響により実際の膜厚は変化します。
目的とする膜厚と使用する液の密度から引き上げ速度を求める場合は式(1)より

同様に式(2)より

と求められます。
※実際には目的とする膜厚に対して、乾燥前のウェット状態の膜厚に換算してから各変数に代入する必要があります。
ディップコーティングと他のコーティング方法との比較
手法 | ディップコーティング | スピンコーティング | スプレーコーティング | ダイコーティング |
コーティングエリア | 両面 | 片面 | 片面 | 片面 |
処理量 | バッチ量によって大量処理可能 | 1枚ずつの処理 | 大面積ワークで大量処理可能 | 大面積ワークで大量処理可能 |
ワーク形状 | 複雑な形状も対応可能 | 平板のみ | 複雑な形状も対応可能 | 平板のみ |
液の消費量 | ロスは少ない | ロスは多い | ロスは多い | ロスは少ない |
液の必要量 | 多い | 少ない | 多い | 少ない |
膜厚分布 | 良好 | エッジ以外は良好 | 良好 | 良好 |
ディップコーティングの場合、一度にワークの両面に大量生産ができるというメリットがあります。
また立体形状のワークも引き上げ方法の工夫により可能になります。
生産に大事な再現性は、液の管理を行うことで歩留まりを上げることが可能になります。